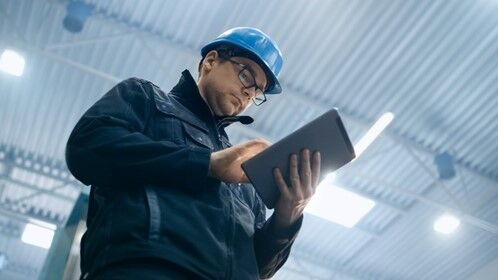
Make TPM Lean and Digital Implementation
- Details
- Category: Newsletters
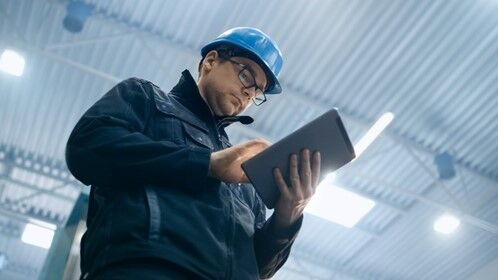
-
The Digitisation Roadmap
The Digital Ecosystem provides a bridge between physical and virtual worlds. This makes it easier to coordinate the people, processes and plant activities involved in manufacturing. This impacts on:
- Performance Drivers
- Real time coordination of labour, material logistics and data provision where and when needed to improve productivity.
- Cultural Drivers
- Enhanced data analysis and modelling of actual vs expected results to optimise current operations and provide the insight to improve future performance.
- Routine administration tasks.
- Automation of usage and performance reporting.
As mentioned earlier, this is a journey not a destination. In part this is because to it takes time to develop new capabilities. In addition to avoid data overload it takes time to find the 20% of information that gives 80% of the control. That involves using the new ecosystem to gain new insights about causal factors and learning how to move away from legacy rules of thumb and historically prudent ways of working. Typically, this also highlights gaps in accountabilities and changes in key roles. See article below.
The first step involves a 3 day hands on training workshop involving cross functional personnel. Suring the workshop they work in teams to apply "Make TPM Lean and Digital" principles to selected live assets. Through this they identify priorities for plant and workflow improvement based on the current shop floor reality. That highlights where improved standards and data clean up activities can deliver the biggest gains. They also identify where gaps in accountabilities need to be plugged.
The outputs from the workshop are used to mobilise a pilot programme to enhance plant and workflow standards and establish a the digital ecosystem for the pilot area.
This typically this involves the use of web based data analysis platforms which have the functionality to link up systems such as CMMS, SCADA, Forecasting, Order processing, Financials. That includes tools to simplify the clean up data, provide intelligent analysis and create charts to make the outputs easier to digest.
This linked up data can then be used to automate routine workflows using low/no code applications provided by Microsoft or others as part of their standard packages. That means goodbye to the spreadsheets developed to collate data from multiple sources.
The use of low/no code applications also provides access to automated investigation cycles to support real time analysis of causal factors and confirmation of countermeasures.
Again the use of TPM and Lean improvement frameworks for pilot and roll out cascades provide a framework to identify and test out how best to do this in a model areas first to create standards and training plans that support the transfer of lessons learned.
Creating the Digital Backbone
The approach used to link up traditional IT systems with web based platforms and applications is known as the Digital Backbone.
For example web based data analysis platforms are designed to combine data from traditional in house IT systems with trapped data (available but not easy to access), stranded data (only available locally) and data from plug and play smart sensors to provide data and analysis to support decision making and performance management.
What we are most interested in tracking is the comparison of actual performance against standards using rule based limits to trigger Notifications where conditions are not as expected or to provide feedback and analysis to support:
- Planning
- Micro planning of materials and resources based on real time activities
- Condition based asset care planning
- Dynamic scheduling /risk management
- Skill matching
- Fault finding and over the shoulder support.
- Optimisation activities to reducing problem hot spots, process pain points and unplanned interventions
The success of the digital ecosystem will depend not only on the technology but also on the skills and experience of individual users.
The lessons learned during the pilot programme are used to update the Operations Blueprint to reflect the insights gained and best practices developed.
In addition the outputs from the Pilot programme includes a phased Roll out cascade to manage the transition to the next Digitisation Roadmap milestone.
Contact us to find out more about how we can help your organisation to implement Make TPM Lean and Digital.
TPM and Lean as Levers to Drive Digitisation Gains
Start by linking up what exists to remove problem hot spots and pain points to achieve more with less effort.
Combining TPM and Lean with the Digital Ecosystem expands the scope of Lean and TPM to include the selection and use of data, analysis and model development to support:
- Top Down Priorities
- Programme Leadership
- Systems Infrastructure
- Change Management
- Improvement frameworks
- Process Review
- Workflow Review
- Learning Process
- Bottom up priorities
- Daily Management
- Real Time Workflow
- Problem Prevention.
The Digital Ecosystem uses Overall Equipment Effectiveness (OEE) data and the Focused Improvement tactics associated with each of the 6 hidden losses to create Digital Twin standards that reflect current levels of demonstrated capability.
Digital Twin Standards can then be used to generate Notification triggers if the reading exceeds a set amount. This stream of information can then be used to support work planning and TPM improvement teams as they systematically reduce the gap between current and optimised performance.
The Lean TPM road map, based on the practices of well respected and award winning organisations, recognises that only around 25% of downtime is due to poor inspection routines. Roughly double that amount of stoppage time is due to
- Accelerated wear due contamination or lack of lubrication
- Human error due to weak work routines, skill and knowledge gaps.
The Digital Ecosystem is used to track and resolve these fundamentals first and then progress through the improvement roadmap steps of:
- Maintain basic conditions.
- Prevent misoperation.
- Enhance process control.
- Task transfer.
- Reduce unplanned intervention/running adjustments.
- Reduce planned intervention.
- Deliver new added value from operations.
SmartTech Improvement Cycles
Adults learn best through practical activity where they can learn from each other.
DEVELOPING DIGITISATION CAPABILITIES
Technology is moving at such a pace that academic courses to develop these skills are always playing catch up. Recruiting people with these skills is also difficult for the same reason. Even when this is possible, one of the biggest tasks involves developing data layers and improving the condition of data. Something that is difficult to do without a good understanding of the business processes.
As adults learn best through practical activity where they can learn from each other, a better alternative is to develop these skills using practical workplace learning projects.
TPM provides Digital Transformation programmes with a practical road map to engage all levels in making progress towards a slicker more connected way of working.
Through that they can identify and deliver the gains come from using the enhance connectivity of digital systems by:-
- Identifying opportunities to use digital tools to leverage the pace of improvement.
- Aligning priorities across functions.
- Supporting teams in real time with the removal barriers to problems.
- Assessing resources to dealing with programme:
- Do we have the right skills.
- Do we have the right tools.
The 90 day improvement cycles develop capabilities through cross functional team using practical projects.
The improved quality of feedback from Digital Notifications combined with the use of data modelling and machine learning analysis tools speeds up development of understanding about how to achieve asset stability. That includes
- Clarifying the notifications that indicate Normal conditions and the response needed to deal with abnormal conditions.
- Providing recommendations for planned maintenance windows
- Providing suggestions for refining process parameters to deal with factors such as variation in material quality or environmental conditions.
This provides practical learning activities for local leaders, front line improvement teams and Senior Leaders as set out in the tables below.
Tools to Provide Leverage for Change
- Programme Leadership
2. Systems Infrastructure
3.Change Management
Define priorities, brief teams and provide support
Creation of the Digital backbone linking systems and processes that coordinate what is done, when it is done and how people work together
Digital ecosystem, work organisation, shared workflows and task transfer.
Tools to Break Paradigms/Improve Added Value.
4.Plant Review
5.Workflow Review
6.Learning and Compliance
Criticality assessment and condition appraisal.
Standardisation, micro planning, skill matching, Material control and over the shoulder support as part of dynamic scheduling.
Job Design, work instructions, standards, learning plans and competence standards to standardise and refine ways of working.
Tools to establish and refine new ways of working
7.Daily Management
8.Real Time Task Management
9.Problem Prevention
Check/Act improvement ideas as part of the daily routine.
Plan, Do improvement activities. Includes administration and coordination of all front line activities.
Capture of problem hot spots and feedback re countermeasures including early problem detection
Early cycles are used to set basic condition standards, reduce equipment wear rates and prevent the causes of human error. In addition to reducing breakdowns, this also improves collaboration between production and maintenance, encouraging new thinking and innovation.
Plant Criticality analysis provides the way to identify what the data can be used for and where additional sensors can be used to drive Notification alerts concerning:
- Basic Conditions,
- Indicate Normal conditions and the response needed to deal with abnormal conditions.
- Recommend planned maintenance activities.
- Contamination control.
- Best practice work routines
- Feedback re problem hot spots
- Confirmation of skill levels
- Work instruction review cycles
- Change request progress
- Work completions
- Compliance control
- Process Control
- Changes to process parameters to deal with factors such as variation in material quality or environmental conditions.
Workflow review activities include:
- Identify and remove non value adding activities.
- Refine complex tasks to reduce the risk of human error and accelerate skill development.
- Automate administration tasks.
- Coordinate the provision of materials and tools based on current status and next planned activity to support dynamic scheduling.
- Provide over the shoulder guidance from specialists as required.
- Make work instructions and task related information is visible at a glance.
The outcome is the removal of functional silos by facilitating the flow of knowledge and skills through the engagement of teams in delivering practical improvement ideas. This also increase responsiveness to change by:
- Reducing bureaucracy and ensuring user engagement to embed new ideas into existing work routines,
- Supporting the design and delivery of more effective ways of deliver customer added value.
"Use Case" Evaluation of new processes and assets.
New or upgrades to systems, assets, products are subject to more formal project governance stage gates during the 90 day cycles covering:
- Concept:
- Idea generation.
- High Level design:
- Proof of concept and specification design,
- Pilot activities to iron out the ideas and project planning to transfer lessons learned,
- Vendor Selection/Pilot Application.
- Detailed Design:
- Collaborating with Vendors on detailed planning and knowledge transfer.
- Manufacture/Procurement:
- Factory readiness planning,
- Includes systemisation of routine work and training for new users.
- Installation and Commission:
- Prove new asset/product/service offering,
- Transition from old to new workflows.
- Full Operation
- Ramp up operation.
- Performance Drivers