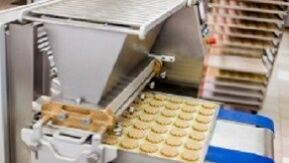
These are:
- Setting direction,
- Building capability,
- Performance management
- Execution.
Click on the articles below for more information on each process and how to benchmark your organisation against these industry leading performers
These are:
Click on the articles below for more information on each process and how to benchmark your organisation against these industry leading performers
If your improvement process could release an hour of shop floor labour what would you do with it? How would that gain be converted into bottom line benefits?
For example, one organisation in the survey delivered the following increase in performance:
The bottom line benefit almost double net profit levels.
In this organisation, although there were technical improvements, around 90% of the gains were delivered through low cost or no cost changes in ways of working.
This included
These gains involved an investment of around 5% of front line team time in improvement activities. Headcount did not increase, the investment in time saved the time to make further improvements.
To deliver the return on investment, first line managers were coached to coach.
Performance management processes were enhanced to incorporate progress of improvement actions and skill development.
On the path to industry leading performance, exemplar organisations develop learning plans matched to two progressive challenges
The outcomes include shared knowledge about cause/effect mechanisms, better improved flexibility.
During the optimise challenge, capability development areas include project management, more in depth anaysis tools to address complex problems involving multiple factors, option evaluation and capital project delivery.
This is characaterised by improved processes to:
In the real world there is never enough time to do everything. That is why urgent items take priority. In an organisation where there is a steady stream of such problems, there may be little time to do anything else.
In exemplar organisations, the role of performance management systems is to align strategic top down goals with bottom up front line delivery of improved performance. It also provides a lever to reinforce core company values and direction.
To achieve this, their performance management processes gives equal weight to
This is characterised by a consistent level of resources allocated to meet problem/improvement accountabilities covering
Operational problems and improvements (allocated to front line teams);
Technical or Support problems and improvements (may require the creation of a cross functional project team).
In this way the performance management process ensure that sufficient resources are directed to the systematic improvement of product process, and management capability.
When Fords plant at Halewood progressed from being the worst to best Ford plant, the shop floor execution routine progressed from one where strangers were viewed with suspicion to one where workers speak to visitors with pride about what they are making. This open proactive work execution culture is one of the distinguishing features of industry leading organisations.
The programme of change took two years. After a further 5 years the site achieved the accolade of best Ford plant by because their programme met 4 principles of engagement
A typical 2 stage road map followed by exemplar organisations on their improvement journey involves:
The early steps of Lean TPM are characterised by enhancing management processes to stop problems from happening. This includes information flows, performance management and workplace discipline which in turn support the improvement in material flow, process flow, labour flexibility and profit improvement.
Traditionally such workflows are carried out through a transient network of internal improvement leaders across the organisation for each project.
Organisations that do this well, formalise this network and support the development of their capability to deliver business transformations set out in the Lean TPM road map. These roles are....
Operational improvements are best carried out by front line team leaders and their teams. They are the ones who can give the attention to detail needed to refine and improve best practice so that they become robust.
Improvement leaders at this level benefit in training for Lean team leaders, Fundamentals of maintenance, Maintenance planning.
As Operational improvements are implemented, technology weaknesses become more visible. Technical resources can then focus on improving process control. This in turn deliver the potential for higher customer added value and flexibility.
A characteristic of this evolution is an increase in collaboration across functions and management levels
Improvement leaders at this level benefit in training for TPM, Lean Maintenance Strategy, Beyond 5S. Engagement skills for managers and team leaders.
The key to long term growth through the introduction of improved new products and services. Typically, this involves working with suppliers to raise standards and collaborate on new products and services.
As each level of capability is achieved and stabilised, new opportunities for further value enhancement become possible. It is this ratcheting up value adding capability and leadership of the customer agenda which helps industry leaders to remain as industry leaders.
Improvement leaders at this level benefit in training for Creating the lean enterprise, Manufacturing Project Management, Early Equipment Management and Innovation
The Lean TPM research generated over 300 improvement journey case profiles. Each had its own story but a number of common themes emerged making it possible to identify an organisations CI journey current status and next steps using just 10 simple points of observation.
Follow the link below to access a simplle Hidden Factory self assessment template covering these 10 points of observation.
Return it to us to receive a free, no obligation benchmark report setting out:
To download the self-assessment template Click here