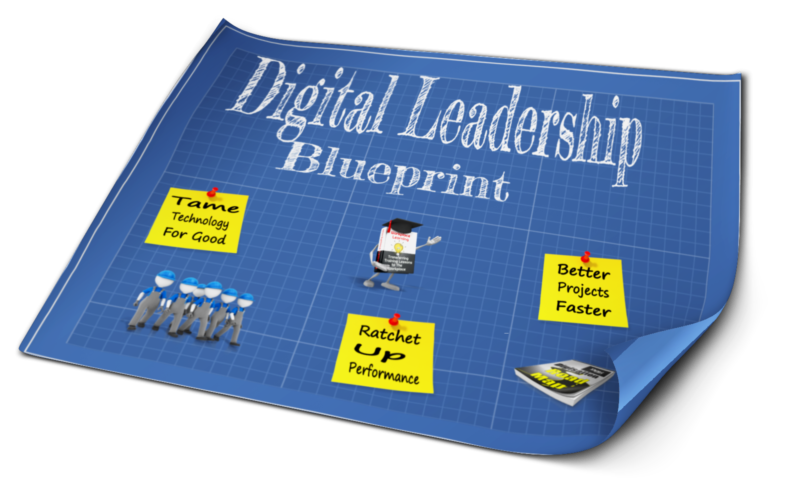
Advances in technology and cloud based software has made it easier than ever to collect and analyse shop floor data and use the results to guide the day to day routine. This creates a digital ecosystem which can deliver impressive gains.
For example, it is not unusual for that introduction to reveal that the true OEE is in the region of 20% to 30% whereas previous reported levels where more than double that.
In most cases, the gains come from actions to:
- Tighten up how planning standards are set and maintained,
- Deal with the pain points such as set up errors that previously led to work arounds,
- Adopt a more joined up approach to work coordination between materials, tooling and resource planning.
That means that the gains were always available. The losses were just hidden from view, usually because of that work arounds that became accepted practice. The same weaknesses also impacts on the quality of other management processes such as those set out in the table below.
The table also sets out the characteristics of weak and industry best practice benchmarks to illustrate the nature of the transition that digitisation can bring.
Unfortunately these processes are closely linked so that changes in any one of these areas will involve changes in the others. Often this involves consolidation of roles, task transfer and the development of new skills.
Management Process |
Common Weaknesses |
Digitisation Best Practice |
Area Management |
||
|
Data is collected and reported to explain the days issues. |
Data is used to optimise current production, understand causal factors and capture lessons learned to ratchet up future performance. |
|
Adhoc problem solving to resolve current issues. |
Cross functional improvement teams collaborate to deliver targeted quarterly improvement goals that align with 12 month business targets. |
Execution |
||
|
Informal work standards |
Systematic improvement to reduce the need for technical judgement and support problem prevention. |
|
Cleaning when needed |
Cleaning is inspection, systematic reduction in sources of contamination at source. Progress towards a clean room environment. |
|
Tasks as defined in Vendor Manuals. Complex, difficult to do tasks carried out by specialists. |
Standardisation categories used to simplify routine tasks. Problem Prevention applied to complex tasks to reduce the need for technical judgement. |
|
Variation in skill levels across shifts and work groups. |
Systemised routine tasks make it easy to establish balanced team capabilities. Intermediate capabilities spread across each work group. Skill matching makes best use of specialist skills. |
Support Functions |
||
|
Frequent replanning to deal with short term issues. |
Synchronised, self correcting workflow. |
|
Informal inspection standards, repair methods and spares management |
Condition based notifications used to stabilise and extend component life. |
|
High level of inspection |
Defined improvement milestones leading to stable operation, reduction in the causes of minor defects and progress towards no touch production |
Table 1: Characteristics of Gaps in the Fabric of Management
Start Small, Learn Fast
Organisations that do this well use the maxim, "Start small, Learn Fast. They treat digitisation as a journey of systematic improvement rather than a one off application.
They have learned that each successful application leads to a higher appreciation of what is possible and with the right decision protocol, that can open up new opportunities for further gains.
For example most component failures are due to accelerated wear caused by avoidable issues like contamination and human error.
Using the Digital ecosystem to deal with this systematically reduce these causal factors by:
- Capturing data to show the cause effect links between cleaning standards and quality defects,
- Designing trouble shooting algorithms that trigger
- Provision of context related information and over the shoulder support where needed
- Quality feedback to refine asset care standards, simplify working practices and accelerate skill development.
In dealing with these issues, Senior Leaders, Local Leaders and their teams learn how to make better use of data, how to share lessons learned and how to make use of new features such as personal dashboards, notification triggers and over the shoulder support.
These practical activities fuel their curiosity about what is possible resulting in "Use Case" proposals for simple smart apps to deal with problem hot spots or deliver further improvement gains.
Developing the Digital Leadership Blueprint
The "Start Small Learn Fast" approach involves the capture of lessons learned as they systematically "Close the Loop" between the physical and digital worlds to systematically build a Digital Leadership Blueprint.
That is structured to set out guiding principles and capture task and role level details to support progress towards desired business outcomes. These sections are:
- Business planned outcomes and measurable goals
- Principles of Operation
- Ways of working (Daily, weekly, monthly etc to support those principles)
- Underpinning systems (to support those ways of working)
- Responsibilities (for those systems)
- Next steps (to build on current best practices)
The Digital Leadership Blueprint is first created as a draft document using the following steps:
- Capture business and cultural drivers
- Understand the current reality and identify the pain points.
- Identify industry trends and diagnosis of internal strengths and weaknesses.
- Prioritise opportunities and develop a road map to deliver the enhanced ecosystem.
- Creation of a Digital Backbone in a model area linking data on traditional IT software with Apps and Cloud based services to:
- Support real time work control
- Provide front line workers with the information and real time feedback they need to do their job well.
- Automate routine task administration.
Detail is then added to the draft Blueprint by capturing insights gained and lessons leaned from practical projects to explore and refining new ways of working using nested daily, weekly, monthly and quarterly Plan Do Check Act cycles.
Below are examples of the type of practical projects undertaken.
Supply Chain Management
Problem: Frequent over production and out of stock imbalances.
The use of digital tools improved visibility of current production and true demand to reduce inventory by over 25% and improve customer service.
Lessons transferred to the Blueprint: Enhance underpinning systems to aid collaboration across the Plan, Source, Make, Deliver stages of the supply chain.
Changes in role of planners to support supply chain data analysis and improve collaboration across functional silos. Delegation of detail planning to front line teams,
Tiered Management Reviews
Problem: Lots of people tied up collecting data, the same topics/issues reappearing on the daily management board.
Digital tools improved clarity, connectivity and consistency of data used in the daily management process.
Lessons transferred to the Blueprint: They found that the biggest weakness was in how to leaders respond to issues from the shop floor and how they close the loop to prevent problems from recurring. This resulted in the development of coaching and mentoring plans for local leaders.
Work Routine Complexity and Compliance Issues
Problem: Inconsistent performance across shift teams due to informal work routines that depended on individual skills and experience
The creation of video micro learning videos and on line SOP creation software led to significant buy in to improving routines.
Lessons transferred to the Blueprint: Changes in process so that updates are implemented within 24 hours of the improvement being identified.
Changes in accountabilities for work routine review, update, authorisation and feedback/compliance protocols.
Contact us for further details of how we can help you to develop your Digital Leadership Blueprint.