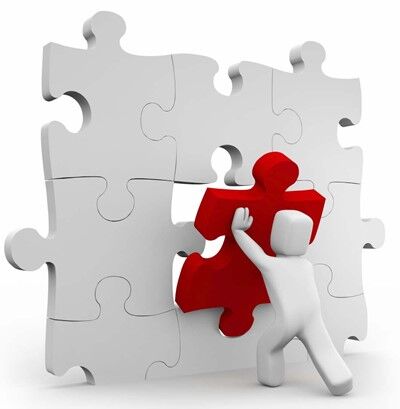
Organisations that successfully deliver lasting improvement, invest time in creating Centres of Excellence by developing workforce capability to prevent the causes of failure, eliminate waste and improve workflow as part of the daily routine.
The Centre of Excellence approach is characterised by the goals that these successful organisations set, for example:
“Year on year improvement in effectiveness by engaging those who impact on it in small group activity”.
This one sentence summarises four interlinked improvement leadership principles:
- Year on year improvement: No matter how good you are today, striving to do better is an essential part of the leadership agenda. New products, new legislation and increased customer expectations means that there is always more to do.
- Effectiveness: is a measure of how well you do what you expected to do. Increasing levels of effectiveness aids plan achievement and releases resource from reactive management actions to improve workflow and value added.
- Engaging those who impact on it: Front line personnel experience first hand the unplanned events and problem areas that impact on effectiveness. Investing around 5% of time to engage them with removing these causes typically achieves an ROI of 15-25% p.a.
- Small group activity: Few of the problems which impact on improvement are resolved by purely technical actions. Countermeasures to more than 80% of recurring problems involve changes to front line work routines and standards. Small group activity involving the right mix of users is the most effective way to surface and deal with these issues.
The Centre of Excellence approach blends the TPM stepwise development of capabilities to ratchet up equipment effectiveness with the Lean thinking tools to drive out waste, improve workflow and remove non added value activities.
The power of the Roadmap comes from the Centre of Excellence development milestones which guide progress towards stable and then optimum conditions (see table 1).
Roadmap Milestones |
Demonstrated Capability |
Competence |
Leadership Agenda |
1A |
Maintain basic conditions and Stable flow. |
Able to reduce accelerated wear and set standards to sustain basic conditions |
Create a stable, organised system underpinned by core competencies across all shifts. |
1B |
Prevent mis operation |
Able to simplify complex processes to make it easy to do right, and easy to learn |
Refine and retrain work routines. Improve knowledge of basic maintenance. Progress towards stable operation and improved workflow. |
2A/2B |
Zero Breakdowns |
Run trials, enhance process control, upgrade visual indicators, transfer routine tasks to front line team. Improve workflow |
Enhance work processes and operating/maintenance knowledge to sustain zero breakdowns. Release time of manager, engineer and specialist personnel to define optimum conditions. |
3A/3B |
Enhance/Automate process control to reduce defects. |
Able to systematically reduce the number of unplanned and planned interventions. |
Reduce adjustment points and formalise those remaining. Use low cost automation to extend MTBI. Systematically reduce the causes of quality defects. |
4A/4B |
Deliver new value from operations. |
Able to deliver a step change in process precision, material yield and responsiveness to shifts in customer demand. |
Support the design, testing and development of new products and services to enhance customer value. |
Table 1: Lean TPM Roadmap Milestones
Progress through these milestones provides leaders with feedback on the effectiveness of actions to progress the difficult to measure factors that underpin the journey to industry leading performance. For example the quality of learning and development.
As research shows, training does not always lead to learning. Most learning takes place in the workplace when people learn from each other. As a result, adults learn best through practical activities and engagement in local collaborative actions to transform the workplace reality.
The outcome is "improvement pull" and the opportunity for leaders to shape outlook and reinforce proactive behaviours.
The importance of this is well illustrated by the words of this CI manager after their programme began to deliver outstanding performance.
"In the beginning of the improvement journey, one of our top Production Managers thought, that 90 % of the reasons for ineffective use of the machinery was due to short term technical problems. Today he recognises that time invested in developing people to prevent problems is the route to high performance."
The Importance of Teamwork and Leadership
As Michael Jordan puts it: “Talent wins games, but teamwork and intelligence win championships.”
Clearly not everything from the sports field translates into the business world there is a clear parallel between winning championships and delivering a winning business performance. Something that is backed up by research which indicates that in business, a team is around five times more effective than an individual at raising performance.
Successful organisations are made up of multiple teams across organisational levels.
These internal improvement Leader Networks exist in all organisations but their presence is typically so informal and pervasive that their importance is rarely recognised.
The Lean TPM Centre of Excellence process is a vehicle to develop this improvement leader community into linked, collaborative all star teams (rather than teams of all stars) by providing:
- Alignment on direction, where there is a shared belief about what the company is striving toward and the role of the team in getting there.
- High-quality interaction, characterised by trust, open communication, and a willingness to embrace conflict.
- An environment in which team members are energised because they feel they can achieve something that matters.
The outcome is the creation of internal improvement leader networks that provide a cross shift, collaborative framework to explore new insights and engage with the delivery shared goals.
Leaders who are more comfortable with a command and control approach will need convincing to try out this approach. Logic alone is not enough to change instincts that have been developed over time.
The LeanTPM Centre of Excellence process provides those leaders with practical ways to experience first hand the gains to be made from coaching their teams to improve the workplace reality.
In successful companies, formalising improvement leader network roles facilitates leading-edge learning, communal competence and a deep respect for the shared experience of capturing and applying lessons learned.
This enhances the way day to day issues are managed and the business processes that underpin that. For example, the table below illustrates the how adopting the Roadmap approach transforms day to day Performance Management.
Performance Management Actions |
Transition from |
To |
Setting priorities |
Reactive |
Proactive |
Use of data |
Reporting results |
Developing insight and capturing lessons learned |
Compliance reporting |
Policing |
Feedback to simplify and standardise |
Risk Management |
Problem solving |
Problem prevention |
Learning and development |
Task driven training |
Systematic skill development |
Performance tracking |
Plan attainment |
Trend against business improvement goals |
Table 2: Roadmap Performance Management Transitions
In that way, progress against the milestones set out in Table 1 above, provides a leading indicator of future performance to close the loop between business planning and delivery of industry leading performance.
This is a quotation from a Continuous Improvement Manager at a 3M site:
“Our regular bottom up team self-assessment against the Roadmap milestones, help us to understand where our strengths and opportunities lie, and this allows us to focus our resource where it can have maximum impact for the company. ”
Next steps?
The first step is a management awareness and review session to assess current status against the road map benchmarks. That includes working sessions to agree barriers and gaps and identify action plans to build on existing capabilities.
That supports the development of a mobilisation programme to launch the pilot phase of the Roadmap programme.
To find out more check out our support programme, send us a message here or contact us via