Resources
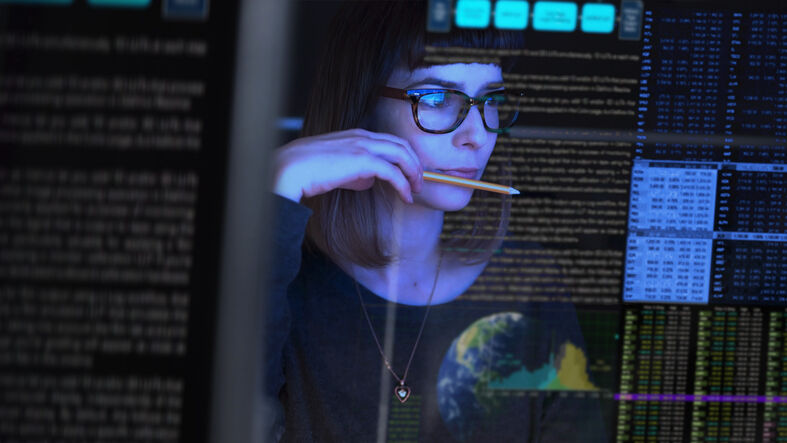
We have put together a mix of self help articles, video's and diagnostic tools. Please feel free to download and should you require any assistance we would be happy to help.
Engaging People with Technology Projects
- Details
- Category: Resources
Connecting the dots around people plant and processes brings out the importance of people in the mix of levers that impact on the return on investment of technology projects. Getting the right people involved improves:
- Decisions about the correct scope of the project, who to involve, knowledge gaps and how to develop Superior Specifications,
- Assessment of and collaboration with vendors to tease out latent design weaknesses, enhance project value and develop Better Project Plans,
- Actions to develop internal capabilities and manage the glide path to Flawless day one operation and beyond.
Avoid common project pitfalls by engaging users at all levels with the following activities:
Applying Early Equipment Management
- Details
- Category: Resources
Most managers and engineers have had first hand experience of capital projects that failed to live up to expectation when introduced and needed significant attention during routine operation. The excess capital costs of these troublesome assets can be huge. Opportunity costs are high too.
Early Equipment Management (EEM) is a collaborative approach to capital projects that will systematically improve your organisations ability to deliver new product, new equipment and new systems better, faster and cheaper.
The TPM Roadmap to Advanced Technology Gains
- Details
- Category: Resources
A common reason for the failure of advanced technology to deliver expected gains is too much focus on the technology and not enough on how it will be used. For example, technology to support condition monitoring is often presented by providers as a way to reduce downtime. The reality is that gains are only achieved when the digital alarm is underpinned with actions to respond to it. In addition, more alarms are not necessarily a good thing because a large number of poorly organized alerts can overwhelm human sensory and information processing capacity.
A countermeasure to this “Siren call” of technology is to link advanced technology selection to the steps of the TPM road map.
Lean Tpm - a Blueprint for Change
- Details
- Category: Resources
Delivering long-term performance improvement is a two part process beginning with…. Creating a sense of purpose
This article, written by Dennis McCarthy of DAK Consulting and Dr Nick Rich of the University of Wales, Swansea, is based on research into why some organisations are able to deliver year on year improvement whereas others, using the same Lean and TPM toolbox, have less success.
Video: Tpm: The Missing Link to Year on Year Performance Improvement
- Details
- Category: Resources
A plain English guide, setting out why TPM is so much more than operator maintenance. The TPM road map is characterised by practical workplace activities leading to increased operational reliability and year on year gains in performance. The practical nature of TPM increases shop floor problem ownership, develops skills and facilitates cross functional collaboration. It is a blueprint for organisational development and cultural change.
TPM was originally translated from the Japanese creators as Total Productive Maintenance. This guide also illustrates why TPM is more aptly translated as Total Productive Manufacturing.
Video: Avoiding Common Manufacturing Project Management Pitfalls
- Details
- Category: Resources
The content explains how to avoid common Manufacturing Project Management pitfalls and deliver superior results from manufacturing project teams.
This covers areas specifically excluded from project management methods such as Prince2 these are
- concept development
- knowledge collation
- Value engineering processes.
- Project plan quality assurance
Factors account for more than 50% of the recipe for success for manufacturing
Video: Delivering Change and Engagement
- Details
- Category: Resources
The most powerful lever for workforce engagement are the conversations that leaders have with their direct reports and managers.
Those conversations are driven by the way in which performance indicators are used. Get this right and it will facilitate workforce engagement so what do leaders need to do to make this happen?
Developing People Centric Leaders
- Details
- Category: Resources
Organisations with outstanding levels of performance achieve that over time through an internal network of improvement leaders. To deliver year on year performance gains, those in key improvement roles such as Team Leaders coach their teams to meet the overlapping performance challenges of::
- Taming Technology
- Raising Operational Performance
- Delivering Business Growth and New Skills
Key skills for People Centric Leaders to master:
- Setting improvement priorities
- Defining improvement tactics and mobilising resources against a realistic and achievable timetable;
- Train and coach improvement team members to progress along that improvement path with confidence
- Enrol and engage those impacted with the change with the compelling need to adopt and refine the improved approach
Find out more about our courses to develop team leader improvement skills