Root causes analysis of over 500 years line production running time identified that 2 factors contribute to 85% of the causes of breakdowns. Both of these are avoidable. The causes are...
- Poor Equipment condition
- Human error
Moving parts will deteriorate over time and as that occurs the likelihood of failure increases from possible to likely. The foundation for reliable operation are the maintenance of basic equipment conditions.
Research into component failure in aircraft identified that random factors contribute to failures. The study was unable to identify causal factors but it was able to confirm that natural deterioration was a factor in less than 4% of components. Further analysis of failures in a manufacturing environment has identified that accelerated deterioration is a significant factor in component failures. This can be due to, for example, contamination or scattering of dust and dirt.
Our research mentioned above shows that reducing causes of accelerated wear stabilises and extends the life of around 80% of components. Further more these components can also be serviced using a condition based trigger. That in turn means that maintenance of these components can be scheduled on before a failure occurs. For that reason condition based maintenance is the most value adding and therefore Lean approach to equipment maintenance.
Another major cause of accelerated wear is Human error. This is responsible for around 50% of component failures including installation errors as well as misuse. In fact the original research into aerospace failure modes identified that 80% of component types are susceptible to installation error.
The factors that contribute to human error risk are:
- unclear or incomplete instructions
- complex working methods
- lack of training.
Developing work routines that are easy to do right, difficult to do wrong and simple to learn not only reduces the likelihood of failure but also provide a vehicle to improve process precision, reduce defects, reduce energy waste and improve material yield. We call this activity Problem Prevention.
Condition Based Maintenance and Problem Prevention are the key to stable operation. That is achieved by the systematic development of best practice for correct operation and asset care by front line improvement teams.
The heart of this process is the Asset Improvement Plan (AIP) template, a toolbox designed to assess, stabilise and then optimise equipment performance.
This template is designed from our work with well known and award winning organisations to systematically remove the root causes of failure to free up time to optimise process capability further.
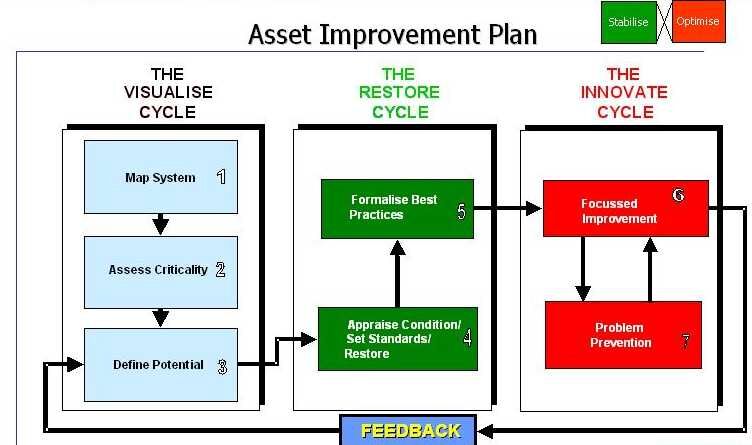
The Visualise Cycle
Helps the team to understand the asset or system under review, how it should work and what its potential is. This cycle provides foundation knowledge to support the development of condition and best practice standards. It also raises understanding of cause/effect mechanisms to supports the development of lasting solutions to equipment problems.
The Restore Cycle
Guides the team in the assessment of asset condition standards and development of best practice for operating and maintaining the asset. This includes the use of Single Point Lessons to structure training and standardise the application of best practices.
The Innovate Cycle
Supports the selections of appropriate focussed improvement and problem prevention tools to systematically increase effectiveness.
Included in this cycle are tools to encourage innovation, improve process capability and apply visual management to make tasks easy to do right, difficult to do wrong.