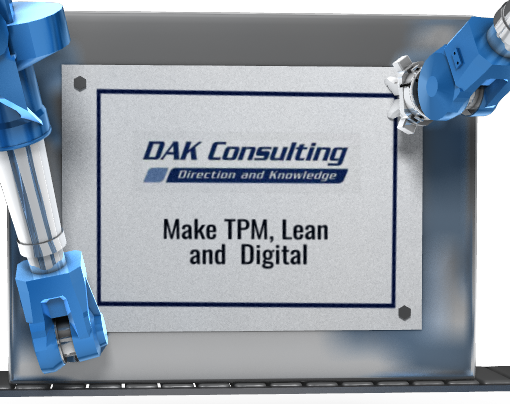
Make TPM Lean and Digital Programme
- Details
- Category: Newsletters
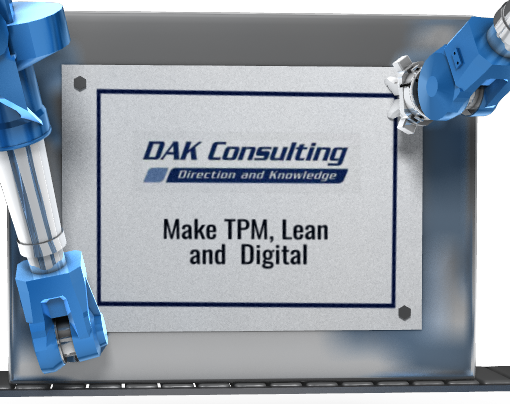
-
The Promise of Digitisation
Imagine a workplace where every process is streamlined and every piece of data is at your fingertips. That's always been the goal of TPM and Lean but it is now much easier to achieve by integrating TPM, Lean, and Digitisation. A programme where you can:
- Use the power of a digital ecosystem.
- Connecting legacy systems and applying machine learning will unveil insights that drive operational effectiveness.
- Craft a new operational blueprint.
- To customise how to use the digital ecosystem to improve current performance and systematically enhance every aspect of future operations.
- Establish a digital backbone.
- Linking legacy systems with web-based platforms to deliver shared workstreams.
- Use this ecosystem to revolutionise plant and workflow effectiveness.
- It becomes the bedrock for boosting productivity and fostering collaboration across value streams.
In addition to performance gains, the transition creates a connected internal network of improvement leaders. The enhanced connectivity and quality of feedback helps them to embed a proactive improvement culture.
Our role is to raise awareness of new opportunities and facilitate the change process. We do that by working with your team to identify potential gains and develop a road map to deliver it. That includes the creation of a new blueprint to define customised new ways of working and develop internal capabilities as part of the day to day routine. See articles below for more details.
Next steps include support for practical projects to demonstrate how to release the synergy between TPM, Lean and Digital connectivity. A journey of discovery where real-time data unveils lost effectiveness, deciphers cause and effect, and validates countermeasures within the daily workflow. That is covered by our Newsletter on Make TPM Lean and Digital: Implementation.
Contact us to find out more about how we can help your team to accelerate the pace of improvement and deliver the full potential of your operations.
Where the Smart Technology Gains Come from
The gains come from linking up systems to create slick ways of working not pockets of technology.
The popular image of Smart Technology typically features the hardware. Robots, 3D printing and Headsets.
The reality is that the gains are not just down to the tech; the true value of Smart Technology comes from how it changes the dynamics of day to day operation, enhancing connectivity between people, plant and processes to transform manufacturing for the better.
Adapting to Smart Technology developments is a continuous path, one that award-winning organisations tread to achieve operational excellence.
This is a journey of discovery where real-time data unveils lost effectiveness, deciphers cause and effect, and validates countermeasures within the daily workflow.
To thrive and grow in this environment involves learning how to use the new ecosystem to identify opportunities to remove waste and release the full potential of the operation. Which is why TPM and Lean continuous improvement frameworks are a key part of the recipe for the successful selection and adoption of Smart Technology.
Creating Your Digital Blueprint
This is a journey not a destination. Create an Operations Blueprint to Navigate Past Legacy Ideas and Adapt to the New Ecosystem.
Digitisation creates a Digital Backbone which links up traditional IT software with Cloud based services and apps to:
- Provide slick systems that meet the complex needs of users across the organisation.
- Automate routine administration tasks and provides information where it is needed based on the task in hand.
- Enhance understanding of causal factors to accelerate progress towards industry leading performance.
- Release management and specialist time to deal with more complex problems such as meeting the challenge of new products, services and technology. Releasing them to manage the future rather than react to past results.
Digitisation does this by "Closing the Loop" between the physical and digital worlds to remove legacy barriers to best practices such as individual systems or data collation by spreadsheet. That changes the day to day reality of internal improvement leaders as illustrated in the table below.
Plant
Workflow
Benefits
Senior Manufacturing Leaders
Fewer unexpected costs, stability of output and resource control.
More flexibility of labour, ease of task transfer, more engaged workforce
Release of skilled resource for other duties,
Local Production and Maintenance Leaders
Routine delivery of planned output, Improved coordination of labour and materials
Higher team morale, opportunities to develop team potential
Reduction in the causes of reactive management, Greater workforce flexibility and productivity.
Support functions
Clearer technology landscape, easier to separate signal from noise
Machine to Machine (M2M) learning to improve productivity and safety.
Reduced risk of human error.
Improved workforce engagement and cross functional teamwork, Shorter skill development learning curve,
Material Supply
Less urgent jobs, more consistent workflow, fewer lost or missing materials
Less inventory to count, fewer reconciliation issues
Reduced quality defect, improved yield.
Production and Maintenance Work planning
Less call for last minute changes
More flexibility of who can do what task
Reduced unplanned downtime and full lifespan use of parts.
Maintainer
Less time on breakdowns
Easy to do routines, time to focus on raising process effectiveness
Simplification of routine complex and difficult to do tasks
Operator
Less unexpected problems
Systematic reduction in pain points and problem hot spots, more autonomy, better job satisfaction
Systematic reduction of complex and difficult to do tasks
That releases time to focus on higher added value activities but the transition of these roles is not automatic. Without a clear plan and support to develop new skills, the risk of resistance to change is high.
To manage these transitions well, our programme involves practical activities that engage those in the above roles in the development of a new Operations Blueprint. That starts with reviewing current practices and setting out ways of working that utilise the new ecosystem.
That highlights where changes in roles and responsibilities need to be supported to raise skills, transfer tasks and deliver those new practices.
This is a journey of systematic improvement rather than an overnight change. It takes time for people to develop new skills and adapt to the new normal. The creation and update of the Digital CI Blueprint is an important vehicle for capturing lessons learned on that journey and aligning the priorities of the internal improvement network at each step.
Developing the Internal Improvement Leader Network
Build Better Working Relationships, Change Outlooks and Establish a Proactive Improvement Culture
In organisations that do this well, the outcome is the creation of an internal improvement network where improvement teams, leaders and support personnel collaborate to develop and share best practices that stabilise and ratchet up performance.
Their role is to engage all levels of the organisations in delivering the gains of the digitised ecosystem by:
- Communicate business priorities
- Envisioning connectivity transitions
- Supporting
- Collaboration across shifts on reducing the causes of breakdowns by tracking progress along the improvement glidepath to guide their teams to sustain basic conditions as part of day to day management,
- Sharing lessons learned to develop their collective skills to sustain basic conditions and prevent mis operation.
- Best practice development to reduce recurring problems
- Transitions of roles to release time for higher added value activities
- Value management plans target investment at the right areas and deliver enhanced customer value to support business growth
The development of this internal improvement network is a central part of Digitisation programme. That provides the vehicle to transfer the lessons learned from the pilot programme to the rest of the organisation.
That systematically develops front line capabilities and releases specialist and support function time to:
- Identify opportunities to use digital tools to leverage the pace of improvement.
- Align priorities across functions.
- Support teams in real time with the removal barriers to problems.
- Identify resources such as the roles, skills and tools to support each step of the programme.
That change of focus also develops internal support function capabilities as set out in the table below.
Traditional roles
New Digital Ecosystem Accountabilities/Skills
Purpose
Front Line Roles
Define and track data capture points to support administration, coordination and early problem detection. Includes providing feedback on problem hot spots and the effectiveness of countermeasures.
Plan/Do support to enhance current performance and translate user experience into best practice plant and workflow routines. That includes work on digital "Use Case" specification and task transfer.
Local Leaders, Quality and HSE managers
Translate business goals into local improvement actions. Includes specification development and testing to confirm "Use Case proof of concept" and transfer of lessons learned across the operation.
Check/Act support to facilitate data clean up and analysis to improve insight into causal factors and refine Decision Models to enhance future performance.
Process Engineering, IT and CI
Solution architect, data engineering, analysis and cyber security, identify available and needed data capture points. Support introduction of Standardisation, micro planning, skill matching, Material control and over the shoulder support as part of dynamic scheduling.
Oversight of Digital ecosystem, work organisation, shared workflows and task transfer. That includes system linkages, data structure and analysis. Support development of user dashboards and microservice applications as part of job design, work instructions, standards, learning plans and competence standards to set and enhance ways of working.
Production coordination and planning
User experience enhancement. Includes oversight of low/no code app development to automate routine workflows.
Ensures user experience supports business goals,
Enables data exchange and system/app integration for routine planning and scheduling tasks.
Table 1: Making TPM Lean and Digital Improvement Network Roles
Avoiding Common Pitfalls
A common reason for the failure of advanced technology to deliver expected gains is too much focus on the technology and not enough on how it will be used.
For example, technology to support condition monitoring is often presented by providers as a way to reduce downtime. The reality is that gains are only achieved when the digital alarm is underpinned with actions to respond to it. In addition, more alarms are not necessarily a good thing because a large number of poorly organized alerts can overwhelm human sensory and information processing capacity.
A countermeasure to this “Siren call” of technology is to link advanced technology selection to the steps of the TPM road map.
Although often presented as purely operator maintenance, TPM has the goal of “continuous improvement in effectiveness through cross functional teamwork”. At the heart of TPM is a process to engage production, maintenance and relevant support functions in working through a structured road map to firstly stabilise effectiveness (zero breakdowns) then optimise asset performance.
Underpinning the road map process, is research which highlights that only around 25% of downtime is due to poor inspection routines. Roughly double that amount of stoppage time is due to
- Accelerated wear due contamination or lack of lubrication
- Human error due to weak work routines, skill and knowledge gaps.
Without improvement to these 2 areas first, advanced condition monitoring is unlikely to deliver lasting gains.
The Journey to Zero Breakdowns
The first phase of the TPM road map involves actions to establish basic condition standards, reduce equipment wear rates and prevent the causes of human error. In addition to reducing breakdowns, this also improves collaboration between production and maintenance, encouraging new thinking and innovation.
An advanced technology tool that supports this first TPM road map phase is the Digital Twin improvement glide path. That is used to compare actual performance against improvement glide path targets which have been set to track the gains from actions taken to improve:
- Basic Conditions,
- Work routines/compliance,
- Contamination control.
The improved quality of feedback from Digital Notifications can then be combined with the use of data modelling and machine learning analysis tools to support the development of understanding about how to achieve asset stability. That includes
- Clarifying the notifications that indicate Normal conditions and the response needed to deal with abnormal conditions.
- Providing recommendations for planned maintenance windows
- Providing suggestions for refining process parameters to deal with factors such as variation in material quality or environmental conditions.
Digital Notifications can also be used to coordinate
- Work instruction review cycles
- Change request progress
- Work completions
- Learning and compliance steps
Find out more about how to remove the causes of unplanned downtime by creating TPM centres of excellence.
Ratcheting up Performance
During the next phase of the road map, the Digital Twin Glide path is used to define and optimise process capabilities to remove the causes of unplanned interventions.
This phase is characterised by actions to understand and eliminate the causes of minor quality defects. In addition to the increased time between intervention, the outcomes includes fewer defects, improved material yields, lower energy use and a greater understanding of the mechanisms that impact on process control.
The gains from the TPM optimisation phase extended time mean time between intervention for one manufacturer such that they were able to run additional night shifts during peak demand months without additional labour. That lowered inventories, increased material yields, improved flexibility to demand fluctuations and reduced development time for new products.
Find out more about what it takes to Ratchet Up Performance here
The application advanced technology as part of a TPM programme could accelerate progress towards such gains from the 3 to 5 years taken to around half of that duration.
- Use the power of a digital ecosystem.